Expertise
DEDECKER PRECISION MECHANICS - DPM is:
- Bar-turner
- Machinist specialist in turning and milling
- Rectifier
With DPM, you have the assurance that all machining and finishing operations are carried out in-house.
Indeed, through our investment dynamics and our desire to offer you a maximum of in-house expertise, we gradually integrate super finishing processes as we develop:
- Deburring
- Honing
- Surface treatments
- Heat treatments
- Specific treatments
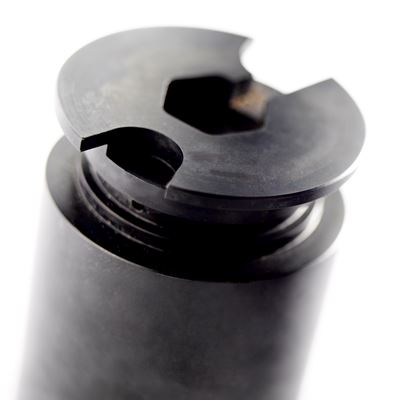
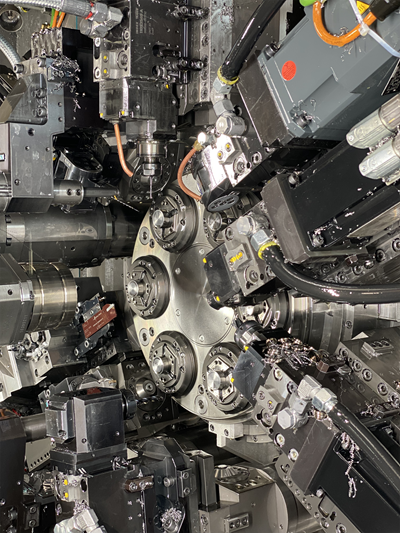
Turning
Bar turning consists of the mass production of precision parts by removing material from metal bars, using a cutting tool.
DPM specializes in metal bars with diameters: < 16, < 25, 32 and 65 mm
To offer you services at the cutting edge of technology, we support investments in our machine park so that they are of the latest generation.
As a result, thanks to very short standard loading times, a reduction to a minimum of downtime, we offer you:
- machined parts at very competitive costs
- numerous machining possibilities: polygoning is possible according to the longitudinal or straight turning process, even on high-alloy materials. , Milling with rotary tool, also in combination with C-axis machining (Transmit function)., Elliptical deburring (Even deburring (uniform chip removal) of transverse bores by interpolation of the C-axis, the X-axis and Z axis with rotary tool.)
Milling
Milling refers to the removal of material in the form of chips due to the combination of 2 movements: the rotation of the cutting tool and the advance of the part to be machined.
Milling using numerically controlled machines (CNC) allows us to produce all types of shapes, even complex ones.
You can also provide us with a drawing or a model to carry out the machining of your precision parts.
Robotic workshop for the machining of parts of Ø > 150 mm from blanks, forgings & castings.
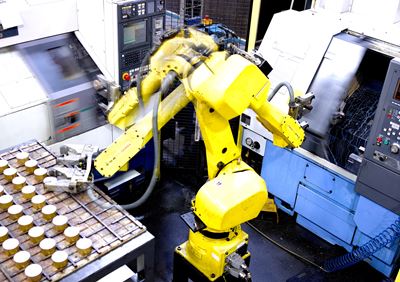
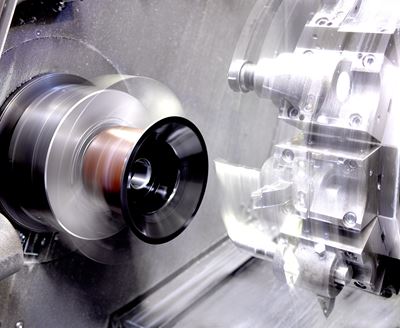
Automatic turning
Turning is also a machining process which consists of obtaining cylindrical or conical parts using cutting tools on lathes, by removing chips.
In turning, the cutting movement is obtained by rotation of the part clamped in a clamp; and the advancement movement by the movement of the cutting tool.
The parts are machined in small, medium or large series on conventional automatic lathes (cam) or numerically controlled (bi-spindles, two or three turrets).
They are machined one after the other in the bar, the aim being to achieve high productivity and precision. We also try, in general, to produce as few chips as possible.
Correction
Grinding a mechanical part is an operation that consists of improving its surface condition. A super-finishing process, grinding is carried out on a machine tool designed for this purpose: the grinding machine. The goal being It is a question of rectifying, ie, of approaching a surface of a perfect form. There are several plane, cylindrical of revolution or conical grinding techniques.
Grinding is often used in order to prepare friction surfaces, for example the seat of a shaft which will turn in a plain bearing or in a seal. It can also be used to give a particular profile to the part when the grinding wheel has previously been machined to the complementary profile.
In the case of cylindrical grinding, the part rotates on itself by performing its stroke parallel to the axis of the grinding wheel.
We are equipped with machines allowing us to offer external grinding from Ø 10 to Ø 120mm.

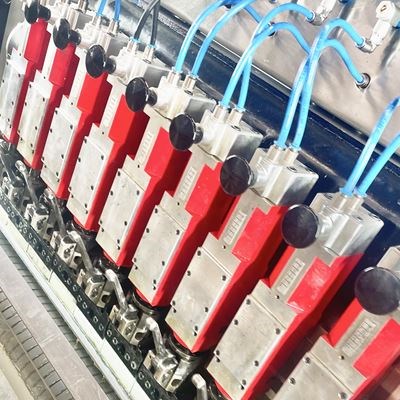
Honing
Honing, also called lapping, is a machining finishing operation which consists of scratching the walls of a cylinder to obtain a smooth and polished face.
Surface treatment
Phosphating is a chemical pre-treatment of steel or cast iron parts. This operation has the consequence of modifying the appearance of the surface of the materials in order to adapt it to given conditions of use.
The treatment consists of a deposit by electrolysis on the periphery of the part and makes it possible to obtain a layer of iron-manganese phosphate or iron-zinc.
DPM offers 2 types of surface treatment:
- Manganese phosphating which improves sliding under lubrication while maintaining good corrosion resistance. This treatment is suitable for mechanical parts that are in friction.
- Zinc phosphating which improves the fixing of paints or varnishes.
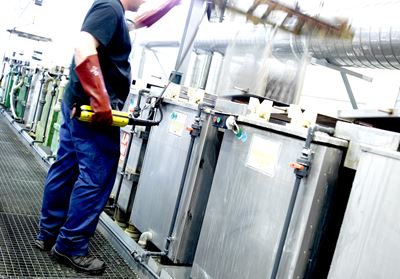
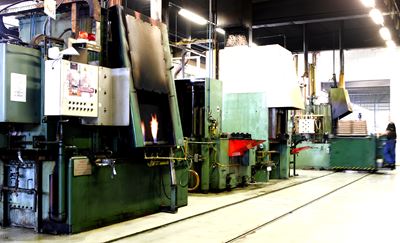
Heat treament
Heat treatment consists of modifying the microstructure of materials such as metals and alloys, i.e. subjecting it to structural transformations through predetermined cycles of heating and cooling in order to improve their mechanical characteristics. : hardness, ductility, elastic limit, service life...
This process is often coupled with the use of a controlled atmosphere during the temperature setting of the part, either to prevent its oxidation, or to carry out a contribution or molecular change of surface.
DPM offers the following heat treatment processes:
- Induction hardening (in a row or between centers)
- Revenue
- Carburizing
- Carbonitriding
- Nitriding
Discover the processes in detail:
Induction hardening consists of the creation of a hardened surface layer which increases wear resistance, surface hardness and endurance.
This process is carried out on localized areas while keeping the qualities of the component.
Tempering is a second hardening process that takes place after quenching and achieves the desired hardness of the surface.
Cementation, a hardening process, is a thermochemical treatment that allows the properties of a metal to be modified by combining it at very high temperatures with cement. The properties of the metal are thus modified.
Carbonitriding is a thermochemical treatment of carbon and nitrogen diffusion. Carburizing process, it allows the increase of the wear resistance and the hardness of the surface by the creation of a hard surface layer.
Nitriding is a thermochemical treatment process of nitrogen dissolution and precipitation of hard nitrides used. It increases wear resistance, surface hardness and endurance.
Specific treatment
The QPQ treatment (Quench-Polish-Quench) is a salt bath treatment that increases the hardness of materials such as steel. It also increases:
- wear resistance
- rigidity
- corrosion resistance
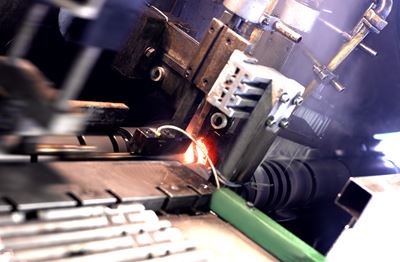
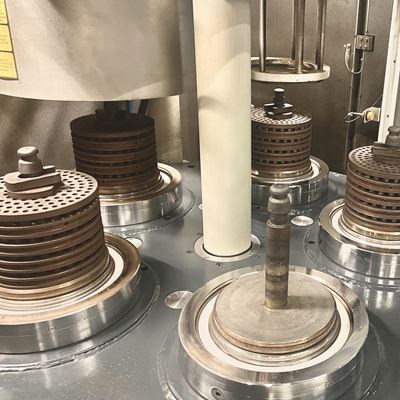
Deburring
During the manufacture of parts, burrs, involuntary surplus of material, can appear. These unsightly burrs can prove to be sharp and thus create blockages during subsequent assembly operations.
Deburring is therefore a machining process that consists of treating the surface of a part in order to smooth it perfectly. The results obtained will depend essentially on the method and the materials used.